
Podcast: The Evolution of Robotics and Prospects for Maximizing Adoption, With Rian Whitton
The first industrial robots appeared in the early 1960s and were initially optimized for production lines. These days, innovation in robotics is progressing rapidly as sophisticated localization and mapping enables improved robotic mobility, and as new levels of flexible manipulation allow robots to perform more specialized tasks. Rob and Jackie sat down recently with Rian Whitton, a strategic technologies analyst at ABI Research, to discuss the evolution of robotics and the implications productivity.
Related
- Robert D. Atkinson, “In Defense of Robots,” National Review, April 2017.
- Robert D. Atkinson, “Robotics and the Future of Production and Work” (ITIF, October 2019).
- Robert D. Atkinson, “The Case Against Taxing Robots” (ITIF, April 2019).
Auto-Transcript
Rob Atkinson: Welcome to Innovation Files and I’m Rob Atkinson, founder and president of the Information Technology and Innovation Foundation. We’re a DC-based think tank that works on technology policy.
Jackie Whisman: And I’m Jackie Whisman, I handle outreach at ITIF which I’m proud to say is the world’s top-ranked think tank for science and technology policy.
Rob Atkinson: This podcast is about the kinds of issues we cover at ITIF from the broad economics of innovation to specific policy and regulatory questions about new technologies. And today we’re going to talk about a new technology or a new-age technology and that’s robotics. In our view, the use of robotics will increase productivity and has the potential to bring back manufacturing production work to developed countries. There’s a lot going on in robotics, in my opinion, probably the most important technology for the next 20 years. And we really have a great guest today to talk about it.
Jackie Whisman: Our guest is Rian Whitton, he is a Strategic Technologies Analyst at ABI Research. He provides consulting and analysis of robotics, automation, intelligent systems, artificial intelligence, and machine learning. He has also written extensively on the commercial application of unmanned aerial vehicles. Subjects of interest include lethal autonomous weapons, unmanned systems, aerospace innovation, and how it relates to international affairs. Welcome Rian, good to have you.
Rian Whitton: Thanks, it’s a pleasure to be here.
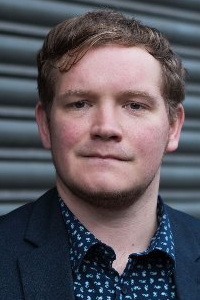
Jackie Whisman: It’s Rob’s favorite topic so I don’t know if we’re going to have enough time, but we’re going to do our best.
Rob Atkinson: It is my favorite topic. I love robots. I know a lot of people don’t. I love robots. Every time I see a robot, I get happy. I was in sort of a robotic device this morning, it’s called an automatic elevator. The old days, they used to have a person that did it, now it’s robotic and it didn’t crash. It was amazing. So we hear a lot about robotics these days, even though they’ve been around particularly industrial robots for many decades. Rian, what’s different now? Why are we hearing so much more about robotics? What’s changed? Why are we seeing both broader and deeper adoption across sectors?
Rian Whitton: Yeah, I think as you say, robots have been a feature for our lives for many years. I mean the first industrial robot really goes back to 1961. It’s invented by Joe Engelberger and George Devol at Unimation. The company is set up in Connecticut and it’s first debuted at a trade fair in Chicago, and then it’s first deployed in New Jersey. So it’s really a story of American innovation along the side the innovations at Bell Labs or in aerospace and so forth. And then it’s very heavily located in the automotive industry and then to some extent in the electronics industry. And for variety of reasons, but perhaps we’ll get onto the robotics industry shifts drastically to Japan, East Asia and Germany and away from the United States because these countries invest a lot more in optimizing the technology. They focus a lot more on automating their production lines. And for that reason, although industrial robots was really invented in the United States, it’s really an international technology with lots of clusters spread all over the world.
I think what we’re seeing today is been kind of innovations in two major groupings. When we’re talking about modern robots, they’re either centered around mobility, so they’re either talking about wheeled systems, maybe track systems or quadrupedal or bipeds, or we’re talking about manipulation. Robots that are palletizing or picking something or doing some dispensation of some kind or doing some material removal. When it comes to mobility, the robots that we’ve seen since the ‘60s have really been automated guided vehicles that have generally run on external infrastructure, magnetic tape, fiducial markers, QR codes, and the like. These pertain to like the Amazon Kiva Systems of which there are about 350,000 deployed now.
But over the last 20 years or so, we’ve really seen the maturation of technologies that are centered around localization and mapping, which have made it much easier for robots to be deployed with sensors on the systems themselves. So that they can navigate without the need for a really rigid physical, external infrastructure. And this creates a real opportunity as it pertains to deployment because you don’t have to build all this external infrastructure alongside the robot. And we’re seeing this with Amazon, their new subset of mobile robots that they’re going to be deploying over the next 10 years will be this new category of mobile robot or what we’re calling AMR.
When it comes to manipulation, the innovations have been similarly quite impressive. You have most industrial robotic arms run on six degrees of freedom. We’ve started seeing systems being built that have seven degrees of freedom. So extra levels of flexibility. It means that the motion planning software can catch up to the tasks that are required of this robot so that they can do more specialized tasks like bean picking with highly randomized objects and SKUs. We’re also seeing cobots coming to the market. These are industrial robotic arms that generally have significant force limitations or force talk sensors applied to them, so that they can work in and around people.
And actually the development of these cobots was really pushed forward by US health regulators and by American universities who kind of saw the backbreaking work that was happening on American production lines in the ‘90s, and actually sort of pushed automation vendors and automotive players to say, “Right, you need to develop some new automation systems that are going to be able to collaborate and work alongside humans rather than simply replacing them.” So those are the two categories in which I would say there’s been a really significant innovation and that’s how I’d probably define the current industrial and commercial robotics industry.
Rob Atkinson: So we could go in a lot of different directions, but one that I think is interesting, you mentioned that there’s really sort of two main types, there’s the mobile type and then there’s the fixed type that are pick and place or cut something with. Increasingly we’re seeing robots in agriculture picking apples for example, those would be kind of a combination of those because they have to be able to move, but then they’re also doing routinized tasks?
And in fact, I was on a panel with somebody from the California Department of Agriculture talking about AI and they’re actually using AI to train so they know which apple is the ripe apple and which apple is not that sort of thing. Can you talk a little bit about that if you’re familiar with that?
Rian Whitton: Yeah, absolutely. So really this category is what is generally termed mobile manipulation. So applying a manipulation device onto a mobile robotics platform. Now the economics of this are very challenging at the present time, in so far as you’ve got a very expensive arm on a very expensive platform that at the moment, at least in industrial environments, hasn’t been seen to justify the cost that it takes to replace a human worker or picker. But as you see and people have talked a lot recently about labor shortages, particularly in agriculture, both in the US and in the UK, post-Brexit. You might start seeing a lot more investment going into these technologies. I think that when it comes to the mobile manipulation opportunity, it’s currently very nascent. It requires lots of advances in motion planning software and the algorithms that are able to match different items or essentially help the robot or end-effector to manipulate the object still need to be optimized.
I think that when it comes to agriculture, though the opportunity goes beyond picking fruit or things like that. There’s already lots of opportunities when it comes to doing analyses on fields or arable land, chlorophyll content, counting the number of livestock, just doing basic analyses on that with tractors or drones is already a very big opportunity. But absolutely, I think that at the moment, the vast majority of activity that we see when it comes to deployments is in what we call structured environments, indoors, some open to the public, the vast majority warehouses, fulfillment centers, manufacturing centers that are not. But I think as the efficacy of the technology improves, you’re going to see robots being deployed into new environments, namely the smart city where they’re operating within streets and around the public and in the field, particularly around agricultural spaces and in places of external industrial infrastructure like chemical plants and so forth. Mines are another real opportunities.
Jackie Whisman: As we see with really any other technology as they improve, there’s always room for robotics to get better, too. What are some of the most important areas of technical improvements that you think are needed?
Rian Whitton: Sure. I think there’s many, but I’ll focus on three. So one would be perception. The modern mobile robots that we see are increasingly pretty adept at localizing themselves while mapping out the terrain that they’re in. But when it becomes to perceiving the environment, actually getting a semantic understanding of the environment, there’s still a lot to be desired. When we refer to semantics we’re referring to the robot actually understanding, not merely whether there is an obstacle in their way and wherever they need to reroute but is that obstacle a person? Is it a manned truck? Is it another robot? Is it a robot from a different supplier? Is it a robot doing the same task or a different task? Can it expect it to move within a certain time so the traffic doesn’t need to be relayed or does the robot need to come to a hard stop?
I think that as you see much more advances in computer vision and in the combination of 3D cameras and 2D and 3D LiDAR, the ability for the robot to actually get a really detailed semantic understanding of their environment will get much better. That in turn will greatly improve the ability of the robot to act autonomously on its own and will drastically reduce the number of edge cases, autonomy exceptions, they’re generally called where a person has to either remotely or manually come in and set the robot straight because it’s made an error.
I think that another big challenge is interoperability. Everyone is talking about expanding their robot fleet, getting out to the thousands. But if we’re talking about a big company like FedEx take their airport logistics hub, that’s going to involve hundreds of robots doing dozens of different use cases. And it’s going to come from lots of different suppliers. They’ll have very different form factors and there needs to be some common protocols in place so that these systems can actually share information, have a common shared semantic understanding of the environment and actually do task interoperability. Where we’re actually seeing some of these standards be formed is by regionsal robotics organizations like MassRobotics up in Massachusetts.
Now that is obviously highly localized with the companies that are involved there. I think that some companies based in Pittsburgh or Silicon Valley would like a bigger role within that space and in that consortium, but it’s not just American actors that are trying to affect that. You have the German car industry trying to put out their own standard on interoperability for ATVs, that’s VDA 505. So I think that industry standards need to improve so the robots can share information more easily. And so that you can get these diverse fleets actually running effectively.
I think perhaps the third area where there might be room for innovation is gradual supervised autonomy. Well, in structured environments like the warehouse, we expect these robots to run almost like clockwork. When it comes to many cases like ports or mines or in civil cases or in robots involving remote manipulation in industrial inspection and so forth, teleoperation is still going to be a very big part of the robotics market. I mean, we think about the bomb disposal robots, but there’s loads of other use cases where the robot being fully autonomous is not going to be possible. But I think that we are going to move away from remote teleoperation where it’s just one person controlling a robot to supervised autonomy, where a robot might complete a certain set of tasks after which the operator kind of supervises them and make sure that the task is been completed and then okays it to go ahead with the next task.
As well as that there’ll be operating and working with lots of different robots and kind of taking a more supervisory role as opposed to a remote operation role. This will have to be enabled by improvements in connectivity. At the moment the latency demands of that kind of operation are quite strenuous on 4G LTE. I think that’s where something like 5G, as it slowly rolls out will become a very big enabler.
Rob Atkinson: Yeah. Doug Brake at ITIF has done lots of work on 5G and everybody thinks about 5G is faster throughput, I can download my movie. But really the much lower latency, which is essentially between the time you send a signal and the time it gets received is really, really important, particularly in these areas you’re talking about there, Rian. So I want to shift gears a little bit and talk about how robots are being adopted. One of the things that you see this constantly, and I know you’ve tweeted about this Rian on your Twitter account, there’s lots and lots of studies that show that countries that adopt robots actually don’t lose manufacturing jobs because they become more competitive. But when you look at around the world and at who’s adopting the most robots, the International Robot Association comes out with a report every year or two or so.
And we did an analysis, they were kind enough to share their data with us. We did an analysis of that study, where we controlled for the income of a country, as you noted earlier, if you’re paying workers a dollar an hour, 25 cents an hour in Bangladesh or something, you’re not going to be able to adopt robots because you just don’t save enough money. But if you’re in Germany where you’re paying 40 or $50 dollars an hour, the case for adopting robots is a lot higher. So what we did it we controlled for all of that said okay, now that you control for manufacturing wage levels, who’s really leading?
And it turns out it’s not the US, the US is way, way behind as is the UK. It’s countries like Korea, Japan, and Singapore, and even China is hitting, batting above its weight here punching above its weight. It’s adopting a lot more robots than you would expect given its income level. Any thoughts on sort of why we see big differences like that?
Rian Whitton: Yeah, no, it’s a very good point. And yeah, I think what the IRA are doing in terms of that data is incredibly valuable. It’s not surprising that the two most financialized economies and those most casual in regard to industrial strategy and planning and protecting their mobile manufacturing base, the US and the UK, really through the naughties hemorrhage manufacturing employment while countries like Japan, Korea, and Germany protected their industries, invested in automation and really came out much better, relatively.
The situation in the US is certainly subpar or has been for the last decade or so. In the UK, the problem is particularly egregious. It’s not merely that the UK has far fewer robots than its competitors even has a lower robot density than China. In fact, it’s almost a half of it. So I think the UK has 91 robots per 10,000 industrial workers. China has about 187. The US is at 228. The most advanced adopters like Singapore are well into the 800s or 900s. But I mean, UK, it’s interesting you say that the adoption of robots is supposed to be correlated with job losses. That’s what the conventional wisdom would say. But I think from Brookings this came from between 1993 and 2007, the UK, which adopted far fewer robots lost about 50% of its manufacturing employment or decreased by over 50%, whilst Germany’s decreased by less than 20%.
It was a very difficult time for manufacturing in high wage countries because of China’s introduction to the WTO, but it was clear that the UK suffered disproportionately. And yeah, I think as you say the countries that have a strategy and deploy and essentially want to protect their industries when it relates to automotive and now electronics have a much higher density rate of robots and thus suffered much less badly in that period. Where I would perhaps say is that when it comes to the robot density rate, it doesn’t tell the whole story about innovation and relative adoption in automation. The US certainly lags in industrial robot adoption, partly because it’s electronics and automotive sectors are comparatively or have been comparatively unproductive versus German or Japanese competitors.
But if you look at where the innovation is in mobile robots or in the cutting edge, the United States remains and perhaps has even extended its lead. If you look at the Open Source Robotics community, ROS centered in the United States that spun out of Willow Garage, obviously comes from Silicon Valley.
Rob Atkinson: What? I think Willow was actually a Google initiative, wasn’t it?
Rian Whitton: Yeah. And Google is bringing out another platform related to robots in Intrinsic. And then you have a company like Amazon, which has deployed more mobile robots, more AGVs than any company today. In fact, in terms of install base, it might have as much as half of the total mobile robot market. So the US has been astonishingly successful at deploying automation. It’s just only been in the industries where the wind has been in its sails, in its legacy manufacturing base, it’s really lagged. But I think the UK is a much more worrying case of what happens when you ignore or pay insufficient attention to automation.
Rob Atkinson: So we’ve got time maybe just for a few more minutes, but I just wanted to touch base on or touch in on this issue of what I think are very, very kind of Luddite-like proposals around robots and tax and robots and banning them. Daren Acemoglu at MIT he and I debated, he’s proposing that the government tax only robots that displace workers, but not cobots. And only automation robots as opposed to other kinds. Bill Gates has proposed a robot tax, and these are responding to fears about workers losing their job, but they ignore the fact of how important it’s going to be for robots to raise productivity, particularly as we all get older and the baby boomers retire, and the governments are running out of money, we’ve got to figure out a way to raise productivity. What are your thoughts on some of those proposals?
Rian Whitton: Yeah, it’s interesting. I mean, Acemoglu has written some papers which would indicate that automation is actually a great way to mitigate the problems that come with an aging population. So the fact that he’s focusing so much on taxing what he considers bad automation is perplexing. What’s worse presumably the purpose of this tax is to funnel money that will retrain people into new jobs. You’re just not going to get that much money from taxing what is still quite a nascent industry. Where we’re talking about at most in the US slightly over 10 billion in terms of sales and globally, it’s still under 100 billion.
By comparison, if you look at the value of share buybacks for one quarter, it’s exceeding hundreds of billions and it’s trillions every year. If you want to fund retraining programs, that’s fine. But the areas where you’re going to get the sufficient money to fund that will be in taxing individuals to a higher rate or cracking down on tax havens. The idea that automation can solve retraining problems through taxation I think is very bizarre.
Rob Atkinson: Well, we’ll just make the tax super big like three or 400% that should solve the problem.
Rian Whitton: Exactly. Exactly. Yeah. I mean, that’s the job pocalypse, I guess, is the meme here, right?
Jackie Whisman: What should governments do to maximize the installation of robots?
Rian Whitton: Yeah, a good question. I think that obviously maximizing adoption isn’t in itself the aim, the aim is to increase productivity. But definitely, ways you could do it is you could actually create tax credits for CapEx. You could make robotics and automation a separate category for that. You could look at maybe a national investment fund for industrial applications. You could maybe look at what a consortium like MassRobotics are doing at the regionsal level, and try to scale this up to the national level. Generally governments in the US is very kind of light touch when it comes to setting standards on robotics. I think that you may want to get a bit bolder on that. I think that you can look at successful countries like Japan who have their own national robot strategy that started in 2015. You looked through what Japan lays out there it’s a clear set of regulatory reforms and some clear targets about how many robot pilot projects they want, how many robots they want deployed in what location.
Whereas, I think if you look at the UK strategies that have been published by our equivalent the Department of Business Energy and Industrial Strategy, the language is much more airy and much less committal. You know, it would perhaps even some very basic targets, you know, the UK has 80% of Germany’s economy but only 50% of its industrial output. How happy are we with that discrepancy? 30% of UK GDP is based on imports. How happy are we with that? Would we like to get that down to 20%? How might automation solve that? I think if you look at where policy and government intervention has been very successful in regards to automation, you could look to a country like Denmark, very small country. They have this incredible cluster of robotics companies in Odense, in Southern Denmark.
And that really is the combination of one of their major shipping companies, Maersk planning, and to build an advanced shipyard about 25 years ago. And funding and making sizable donations to the local university. Now the actual shipyard didn’t get built, but a lot of that funding translated into the robotics industry which has since been favorably funded by the local government and has really been fostered. And there’s been given a lot of tension, even like basic interactions like getting access to the local mayor who can extend the lease or things like that. And making it a really business friendly environment has really helped this very small cluster make a very big impact on the general industry. You see that in a lot of these Odense companies or two of them specifically, Mobile Industrial Robots and Universal Robots are leaders in their respective fields and have been bought by an American manufacturer called Teradyne.
Rob Atkinson: That’s great. We did an event, I don’t know, maybe two years ago up in the Senate, US Senate, where we had a panel on robots. We actually had a couple of robots actually there and I think one was Universal, as I recall. Rian, this is really fantastic. We could keep going, but unfortunately we are out of time. So I want to thank you so much for being with us really, really interesting.
Rian Whitton: Thank you. It’s a pleasure to be here.
Jackie Whisman: And that’s it for this week. If you liked it, please be sure to rate us and subscribe. Feel free to email show ideas or questions to [email protected]. You can find the show notes and sign up for our weekly email newsletter on our website, itif.org. And follow us on Twitter, Facebook and LinkedIn @ITIFdc.
Rob Atkinson: We have more episodes and great guests lined up. New episodes will drop every other Monday so we hope you’ll continue to tune in.
Jackie Whisman: Talk to you soon.